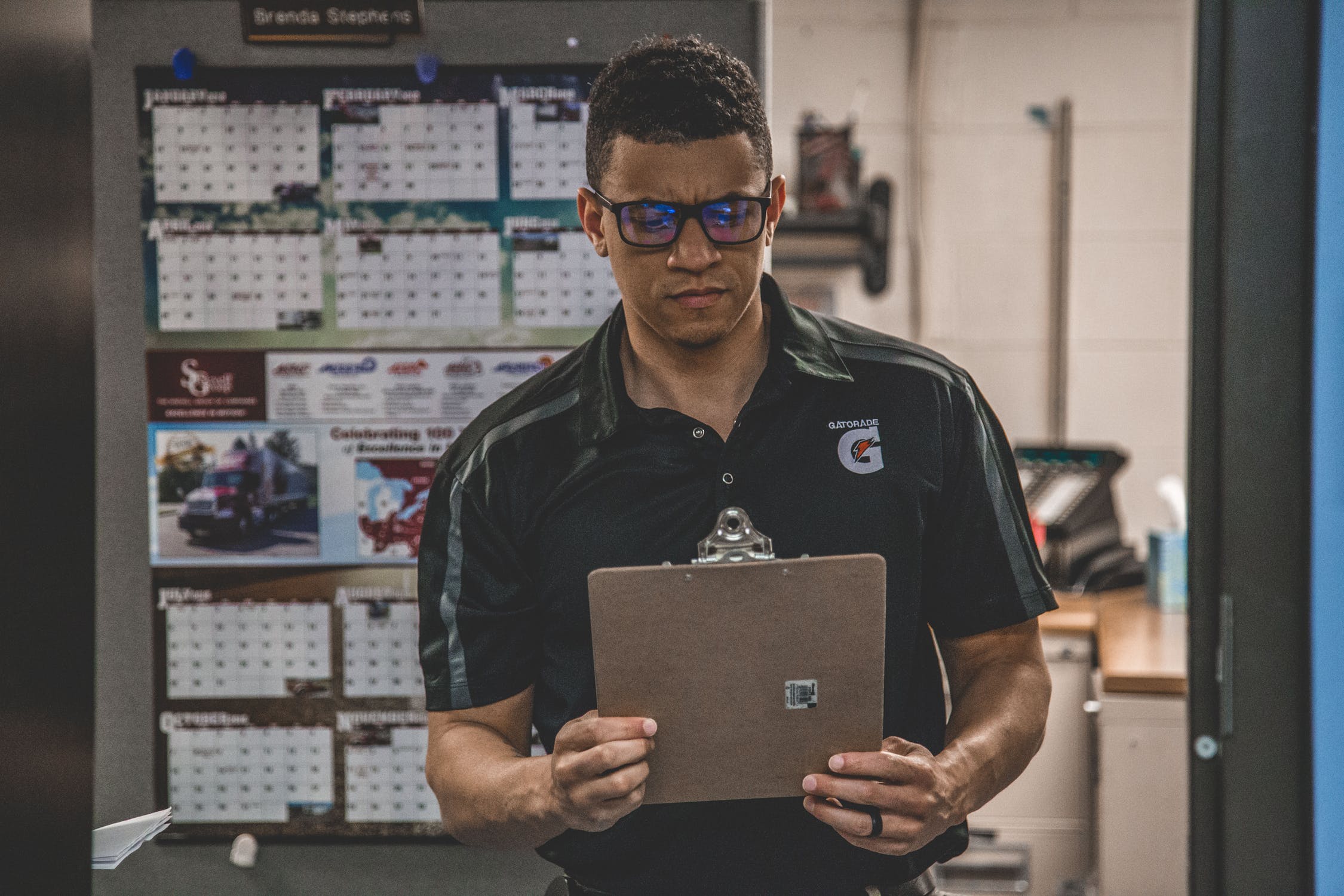
Human errors are a huge contributor to discrepancies in inventory counts, whether it be physical counting errors, scanning errors, product misplacement, or mispicks.
We've gathered our favorite tips: here are 5 simple ways to prevent inventory errors, and thus reduce human error.
1 | Simplify the processes whenever warehouse workers are involved
Simpler actions translate to less error, especially when the action is one performed with high frequency.
2 | Clarify locations
Make sure locations are marked clearly and are easy to get to. The easier it is for workers to access and find the locations, the less time it takes to seek them out and handle them.
3 | Keep locations organized
Make sure that your warehouse workers properly maintain locations. Products can fall out of locations, be mistaken for resting in the wrong location, or be moved to another location entirely without making note of the move.
[Warehouse Management vs. Inventory Management: Which is Best?]
4 | Item labels
Make sure all items are labeled correctly; this may sound like a given, but you'd be surprised how often UPCs and Bar codes can be damaged or wrong (we were!). Keep track and correct these issues as they are stocked and/or picked; no matter how rushed you may be, it's worth the time to fix so as to avoid future customer complications.
5 | Track all items by location
Our final way to prevent inventory errors is instead of organizing inventory by type and manually organizing each time a new item is stocked, instead organize items by location so that there's no re-organization required.